To put it in simple terms, this is a machine that uses mirrors to direct a laser (from a long glass laser tube) down into material. Adjusting the power will scar the surface (engrave) or cut right through the material. The material can be pretty much anything except PVC (dangerous fumes) or metal (60 watts not powerful enough). You can engrave Macbooks, cut hotdogs, or engrave logos on top of your cappuccino.
Before deciding on this machine, I did my research. There are quite a few other alternatives out there. GlowForge, Muse, Dremel… All of them are either smaller (12×20 working area) or much more expensive ($5k+). Being a tinkerer, I decided to take a gamble with this no name “Chinese” laser machine and use the extra money saved to mod/upgrade.
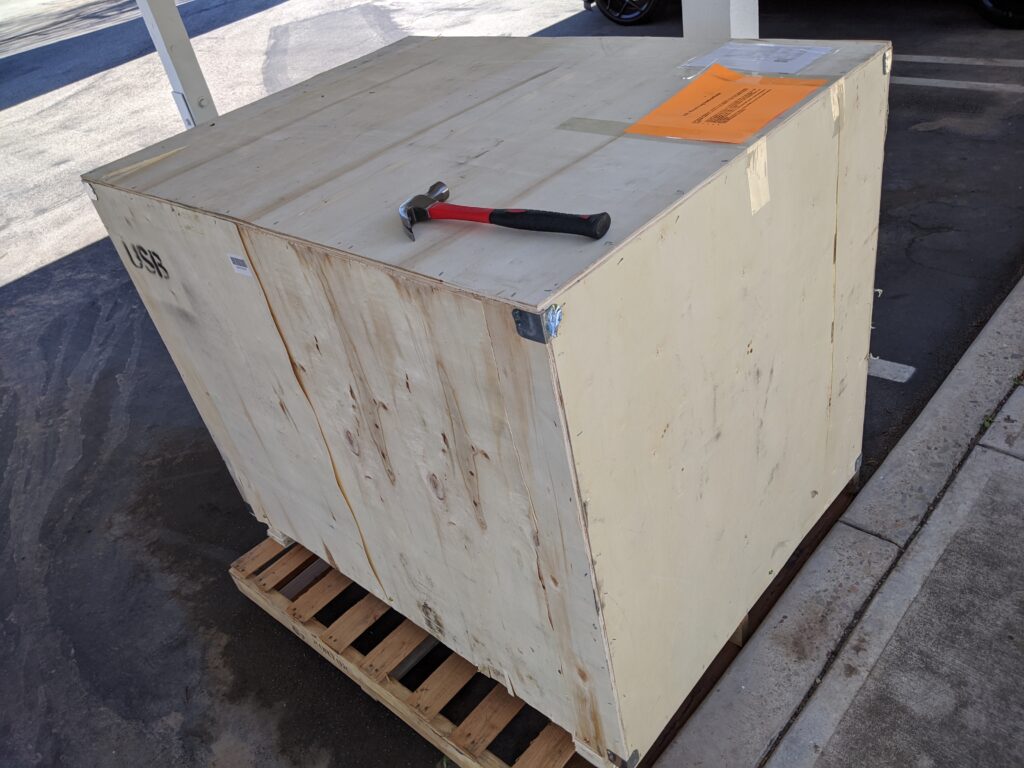
This machine is 500 x 700mm and has passthrough for bigger pieces. You can find it on eBay but be wary of the “free shipping” because I ended up paying $150 for a lift gate service which is a required fee for residential delivery. You’ll need another person to help unbox and move this thing around.
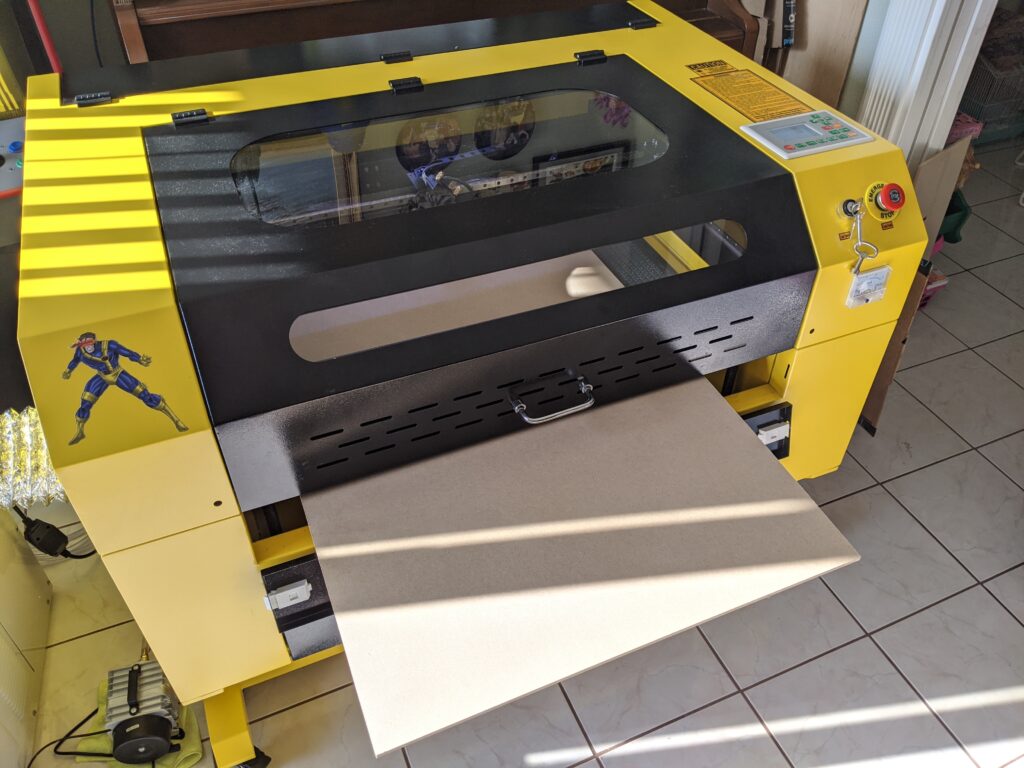
Out of the box, the laser works fine. I was able to do test cuts and some small projects. Being a tinkerer though, I had to mod it to get the best out of it. Here is some information on the mods that can improve your machine if you choose to get it or one similar.
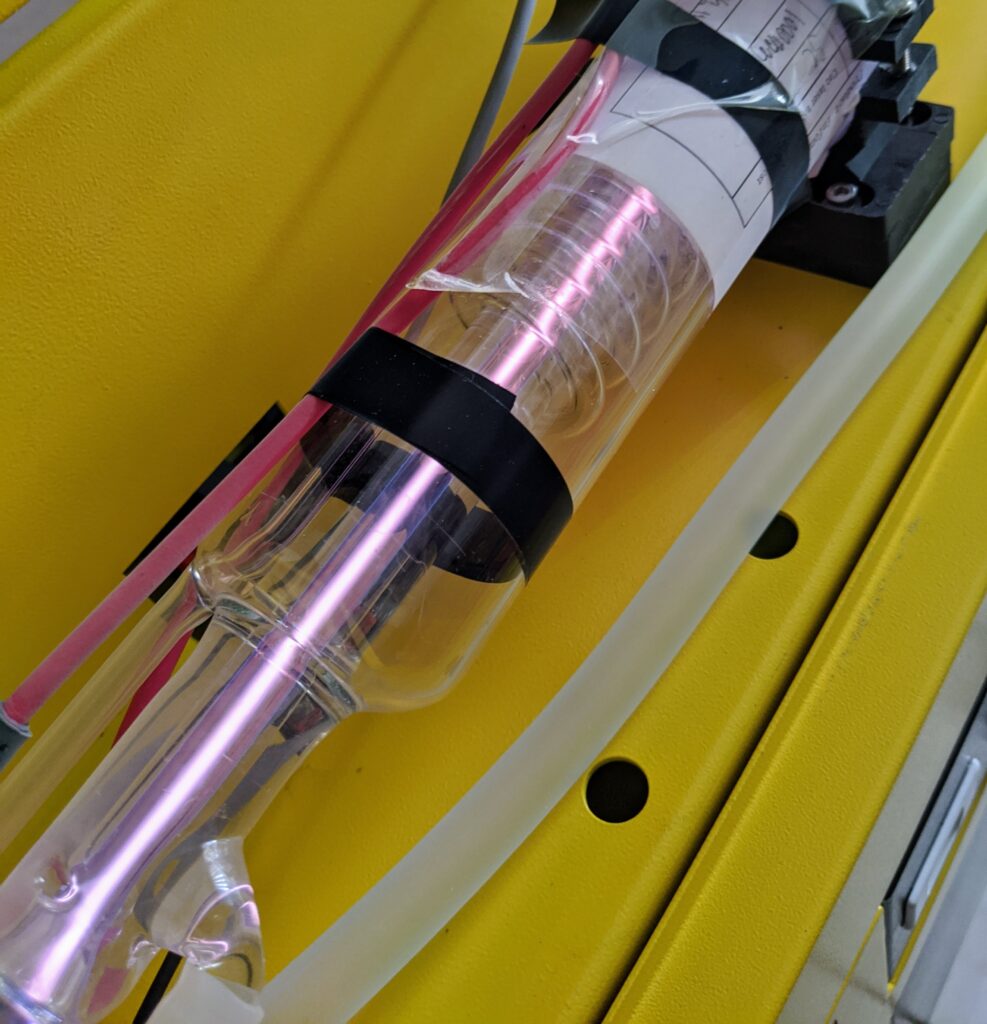
Air Ducts
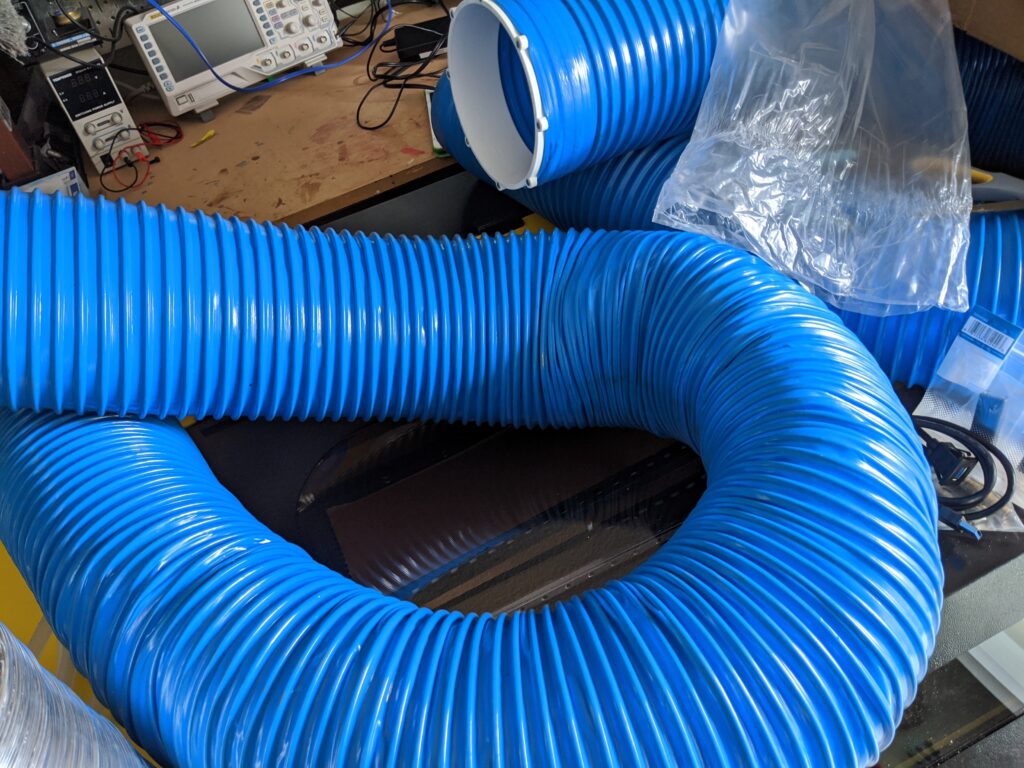
You’re using a laser to burn material so you need good air flow to move the smoke outside. These are the original air ducts that were thick, heavy, and smelled weird. The shape also deformed when exposed to the sun. I decided to replace it with the one below.
This hose is way lighter, can expand and compress well, retain shape better, and was much more pliable but still cheap.
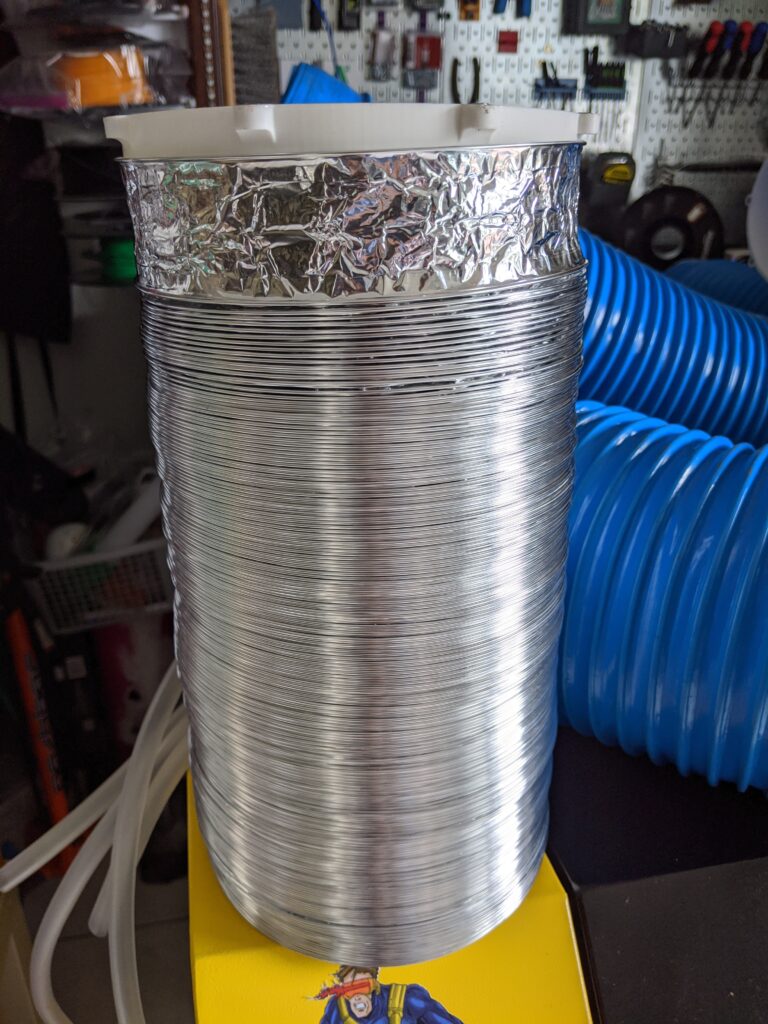
Hoses
The long laser tube has water running through it constantly to cool it down, that means there are 3/8 inch tubes carrying the water. The original tubes that came with the machine were weak, cracked, and smelled pretty bad. After running my machine a few times, I noticed water was leaking from somewhere, no matter how tight the connectors were. I replaced the tubes AND the connectors with brass fittings.
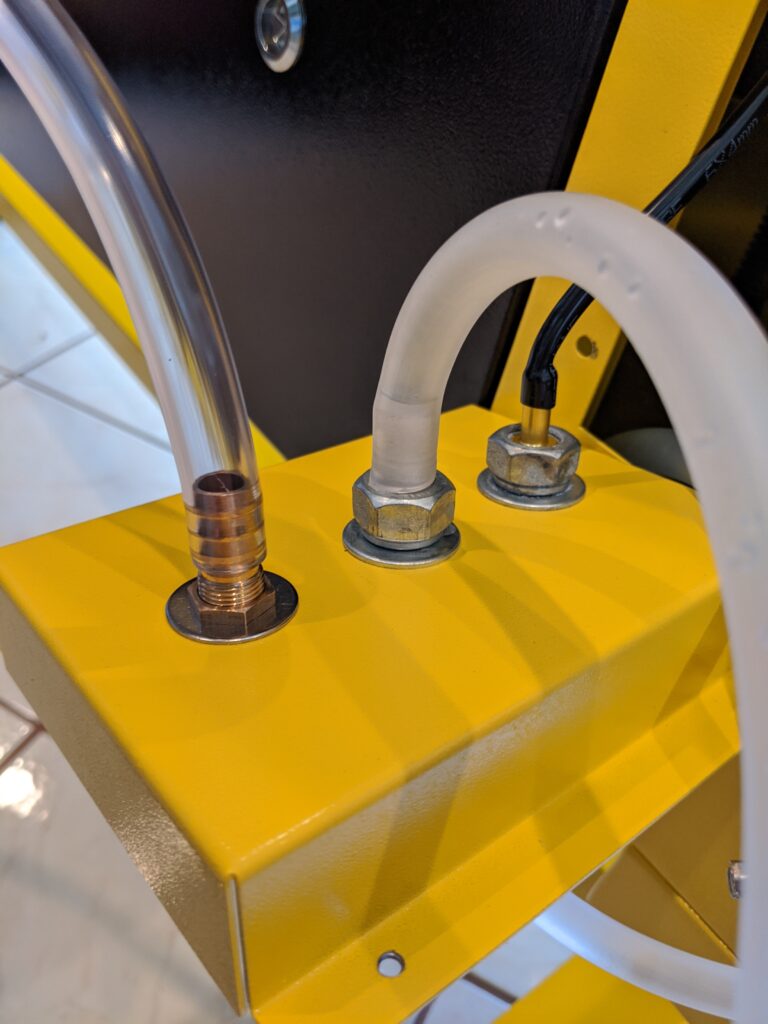
I replaced the tubing with food-grade vinyl tubing. It was a little more sturdy and no more water leaks. The brass fittings were also a huge help, so much so that it didn’t even need the hose clamps anymore.
Rollerflex Food Grade Crystal Clear Vinyl Tubing, 3/8-Inch ID x 1/2-Inch OD, 100-FT
Water Pump
The machine comes with an aquarium-type water pump that pushes water through the laser tube to keep it cool. This will improve the life of the tube and also provide optimal firing. Since laser tubes are expensive, I decided to upgrade to an actual water chiller.
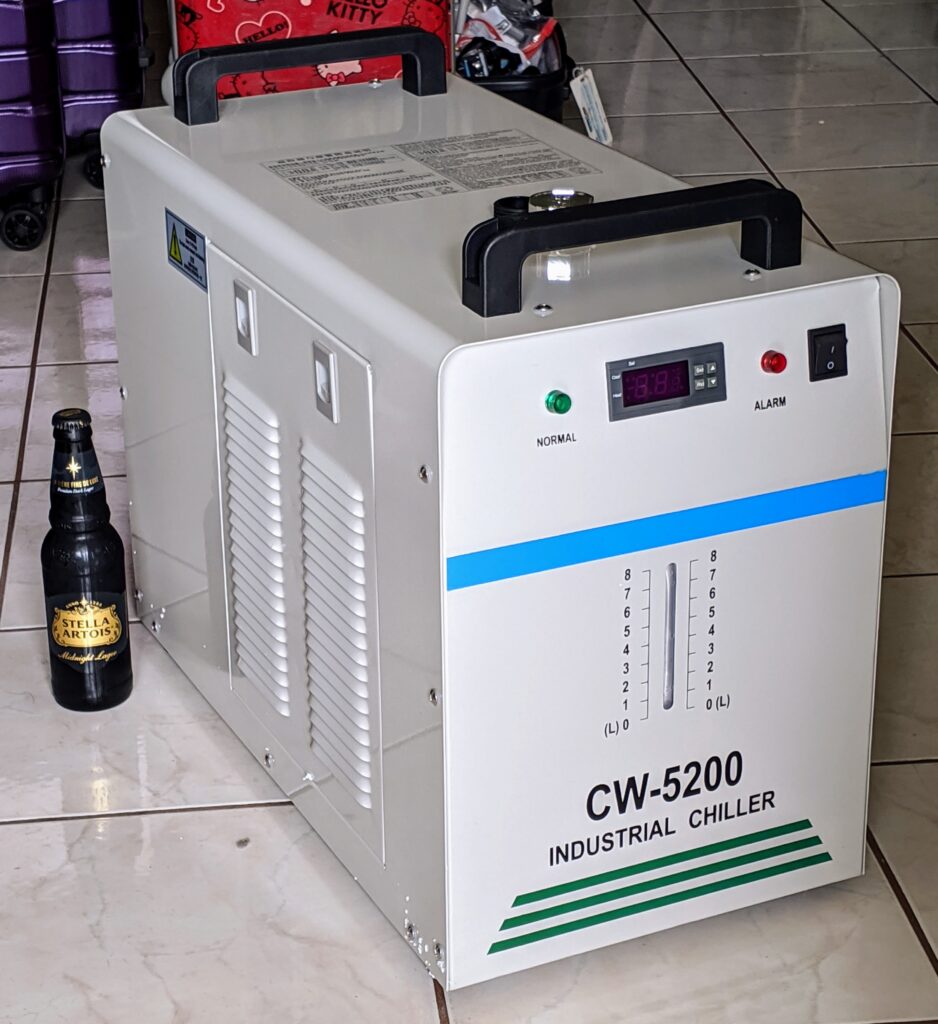
I made the mistake of getting the CW-3000 which does NOT have a compressor and refrigerant. This CW-5200 was expensive, almost $400, but since it’s protecting and extending the life of the most important part of the laser machine (the laser) I decided to add it. The compressor keeps the water at a specific temperature you set, and more importantly keeps the laser firing under consistent temperatures for even cuts and engraving.
Ammeter
At the end of the day, the laser tube is pulling just under 20 milliamps of power. When you cut things, you specify the % power like 20% or 80%. Initially 80% might mean 18mA, but as the tube is getting weak and dying, 80% might mean 13mA. Adding this analog meter will let you keep tabs on the strength of the laser tube.
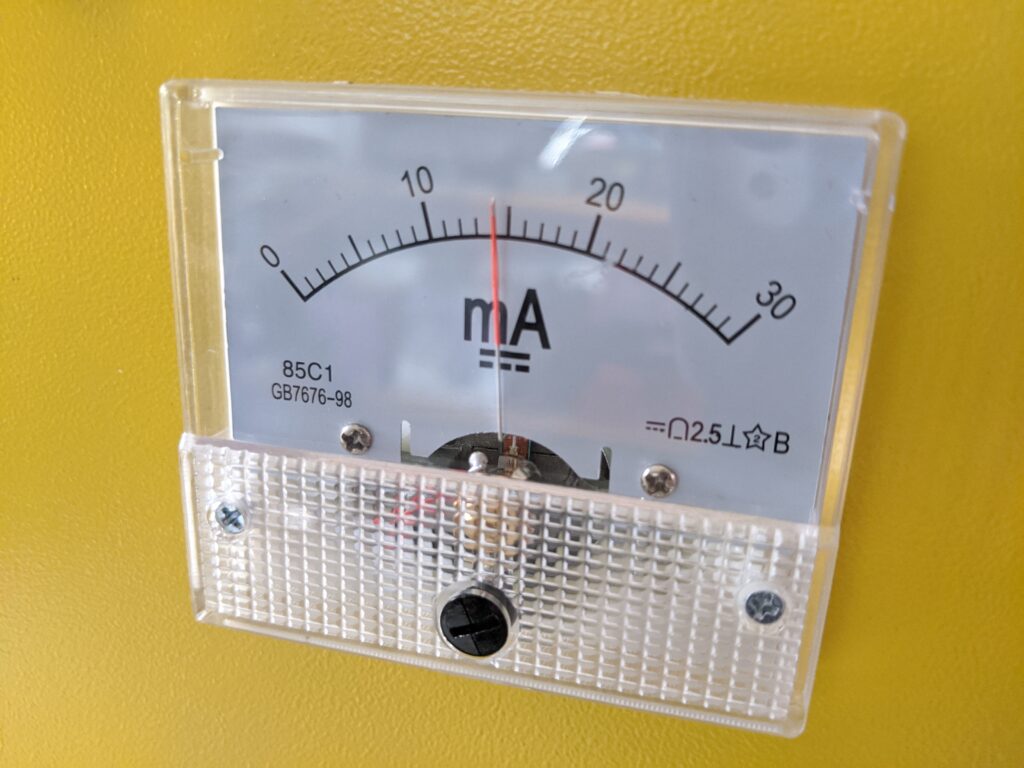
Installing this was a bit of a feat. The metal that the machine is made of is not the thickest, but heavy duty enough to make cutting and drilling through it impossible if you don’t have the right tools. There are plenty of videos online on how to wire this thing. Basically there are 2 terminals, and the current passes through the laser tube circuit.
Fan
The fan that comes with the machine is pretty scary looking. I’m sure it works, but it looked really loud and clunky and took up a lot of space. I decided to get an inline fan with adjustable speeds.
VIVOSUN 6 Inch 390 CFM Inline Duct Fan with Variable Speed Controller HVAC Blower for Ventilation
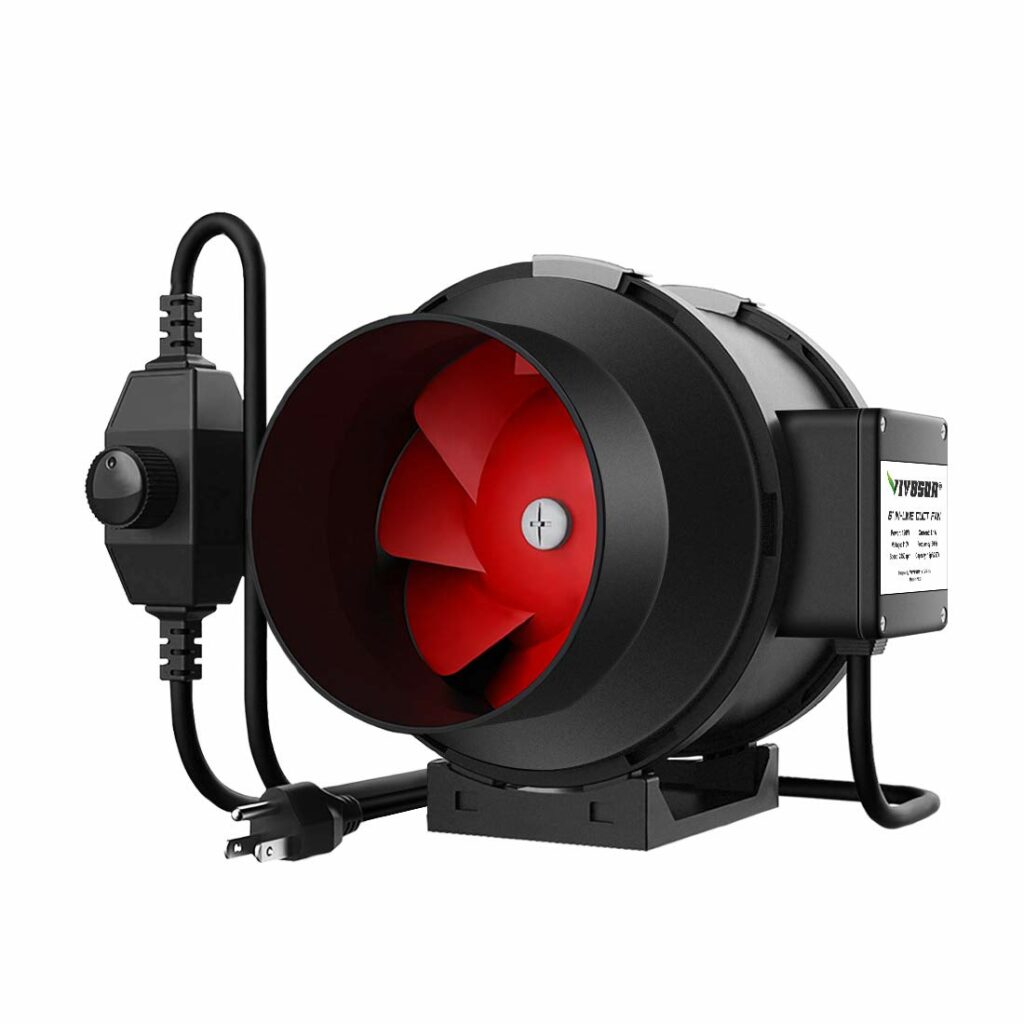
This is pretty optional, but wasn’t that much to upgrade. I really like it, it’s quiet and looks reliable and worked fine with the upgraded air ducts I got.
Lightburn
The RDworks software looked horrendous. After a bit of research, everybody seemed to have good things to say about Lightburn which is a 1 time 2 or 3 computer license for $80. If you want updates after the first year, you need to pay a renewal license, but it seems like as it is, the software is great. Most of the time I design things in Fusion 360, export the drawings as DXF, then import DXF into lightburn. They are basically vector files like Illustrator.
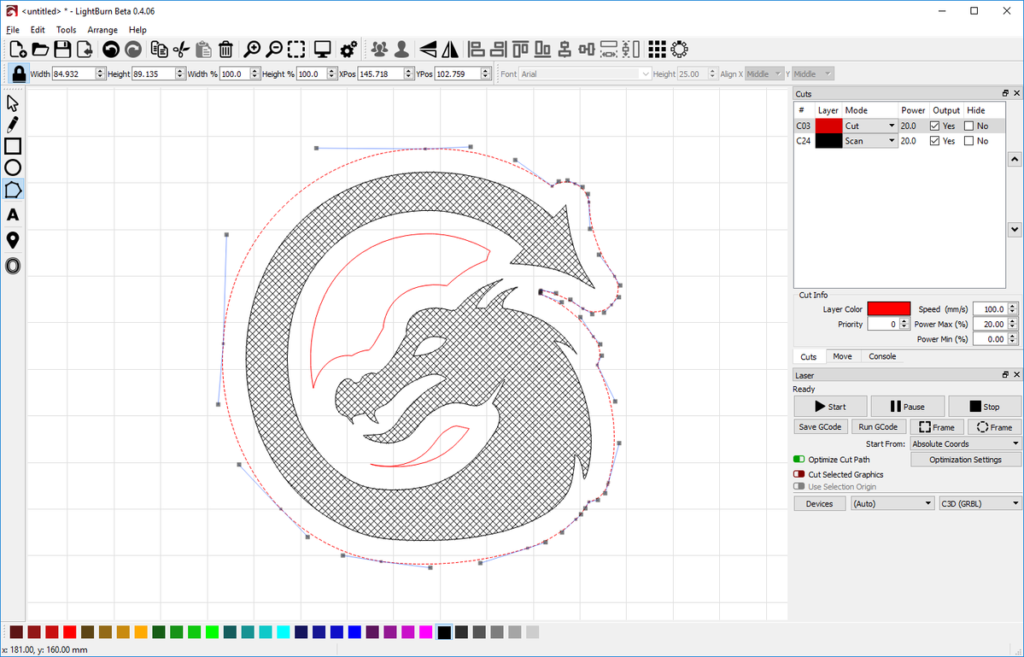
The software works perfectly with my machine’s Ruida controller. It recognized the controller, bed size, zero issues, highly recommended.
Camera
The camera really isn’t necessary, but if you’re using Lightburn, there are some cool features you can do. Glowforge laser machines have cameras. Muse and Dremel also have similar features. This basically allows your Lightburn software see what’s there. You can also take pictures of something and let Lightburn convert it into shapes to cut out. Or simply use it to spot check that you have enough material to cover your cut. Or, if you’re engraving something like a laptop, you can ensure it’s going to be in the right place.
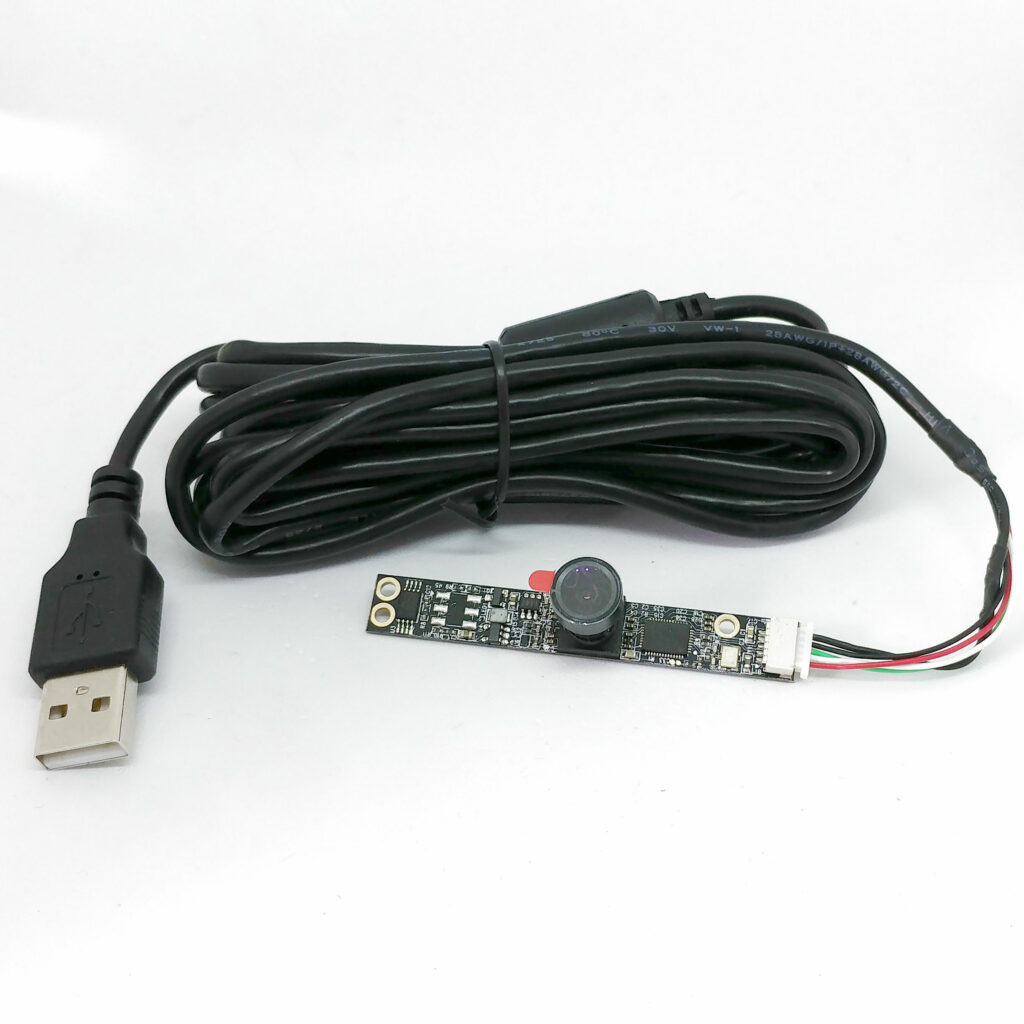
The correct camera to get for this machine is the 140 degree fisheye lens. It lets the camera capture the whole area. Calibration was a little frustrating, but after about 20-30 minutes and multiple tries, I finally got it to “flatten” the image and accurately map out the working area.
Control Panel
This is my own custom upgrade that is currently in progress. With all these things plugged in and running, it was cumbersome to walk around turning things on and off. So I designed this control panel with AC switches to easily control the peripherals and also have a place to plug in the Lightburn camera.
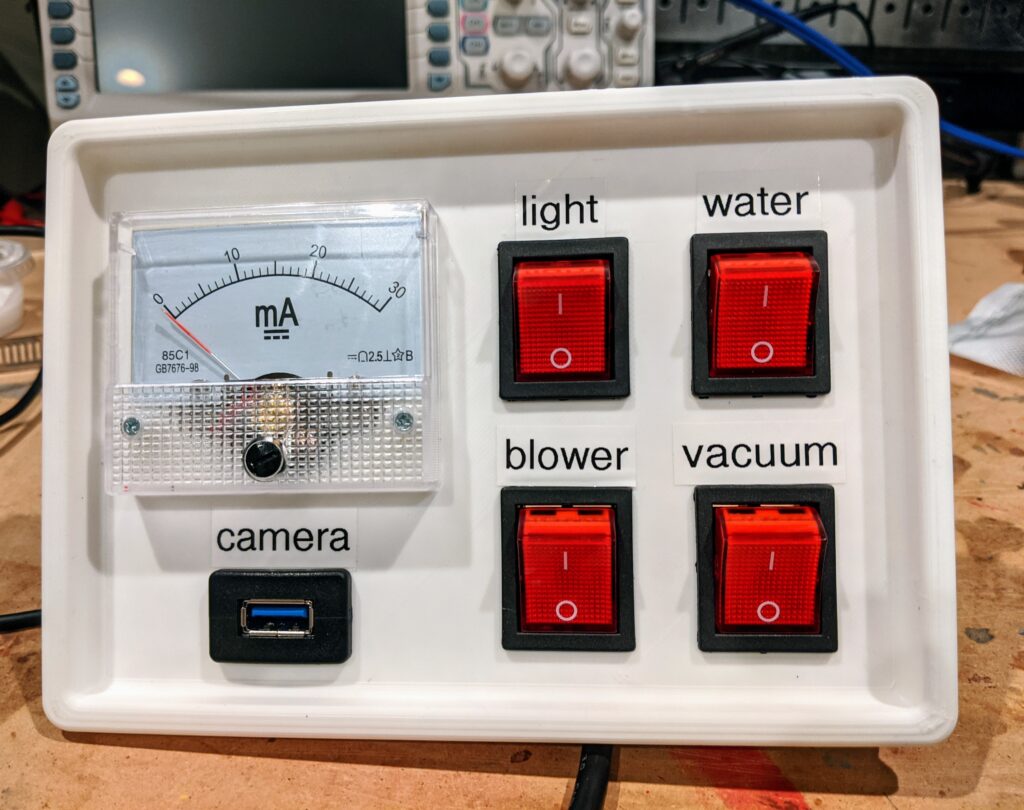
There’s also a switch for “light” because I’m adding additional LED strips inside the machine. There is only 1 small strip of LEDs and I want lights on the other 3 sides of the working area. I don’t need that on all the time so I added a button for it on this little control panel.
Conclusion
This machine has been a dream. It feels so fast to create and prototype things compared to my 3D printer. As you can see from my builds section, it’s keeping me busy. It also allows me to start building larger things (until my CNC machine comes in). It’s like my Cricut machine on steroids.
If you have any questions about it, let me know. More than happy to help and share experience or knowledge.